The automation of field work by robots is slowly taking shape, and the first models are on the road in Austrian fields. This increased use of autonomous systems is leading to a reorientation of the design of machines and equipment in line with the forward-looking management of agricultural land, but is also addressing many new challenges.
Some of the most important challenges in terms of practical use include:
• The monitoring of the quality of the work of the implements and robots
• Fully autonomous operation in the field (legal and technical requirements)
• Interface standards: Hardware and software interfaces for developers of robots & devices for autonomous systems.
• Energy supply for certain types of drive
• Autonomous travel from field to field
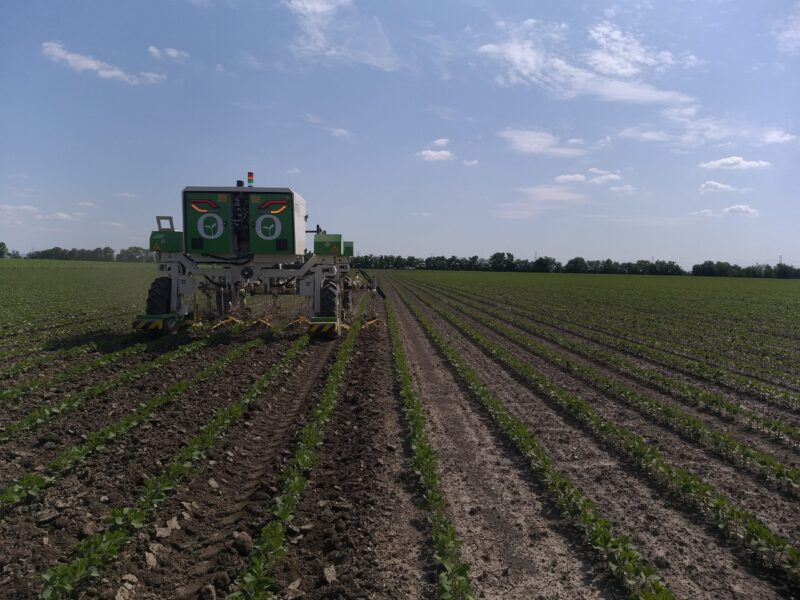
We at the AIL and RWA Farming Innovations carried out extensive field work in sugar beet and soybean in the first half of 2023 with the ORIO implement carrier from Naïo Technologies, equipped with a shifting frame from “Tillett and Hague” and classic lightweight chopping tools.
Findings from our field operations:
Monitoring the quality of work
During our field work, monitoring the quality of this work turned out to be an enormously important factor. Work that is usually done by the tractor driver has to be done by the robot: The assessment of the quality of work and the reaction to it, such as the automatic adjustment of settings, is essential. Often a chopping element can simply be blocked or affected by a stone, which leads to further problems. In such cases, the robot must react. Naïo Technologies is currently developing a system to monitor the quality of the work.
Autonomous operation of robots
The navigation of field robots using RTK GNSS works very well and offers ideal conditions for the autonomous management of agricultural land. However, challenges for autonomous systems include the verification of navigation information using sensor information from the environment (e.g., does the map match reality or not?) and the capturing of safety-related information about obstacles, etc. ORIO’s safety system includes tactile touch sensors (bumpers), laser scanners and geofencing and, from a legal point of view, permits unattended operation. However, this could not yet be tested in practice. The Naïo Companion app is available for communication with the robot.
Interfaces
Several interfaces have already become established in classic agricultural technology but this is not yet the case in agricultural robotics. On the hardware side, ORIO provides a category II three-point linkage for connecting a wide range of implements. On the software side, however, there are unfortunately still no standards for exchanging data/signals with other devices. The exchange of data between robots, including between robots from different manufacturers, will become more important in the future. Due to the limitation in terms of interface design (no hydraulics and pneumatics, etc.) and the lower weight limit of the three-point attachment, only a limited type of devices can be considered for integration.
Energy supply
The amount and availability of energy is a critical issue with electrically powered field robots, as it is severely limited by the capacity of the batteries. With the largest ORIO battery pack, a working time of about eight-nine hours is realistic. This allows for practicable use. However, if there is no direct charging infrastructure at the place of use, the logistics for charging the batteries must also be considered.
Autonomous driving from field to field
Autonomous travel from field to field is another important aspect of the large-scale integration of robots into the agricultural work process.
The robots must be able to meet the requirements and expectations of the customers, because it is for them that they are developed. Through our first deployments of a practical system on a farm, we were able to gain important experience that we will take into account in future decisions in the field of agricultural robotics at RWA and the Lagerhaus cooperatives.